Smart 200L Drum Filling System Touchscreen Controlled & Fully Automated
Smart 200L Drum Filling System: Touchscreen Controlled & Fully Automated
Overview
The Smart 200L Drum Filling System is a state-of-the-art, fully automated solution designed for high-speed, precision filling of 200-liter drums. Featuring an intuitive touchscreen interface and advanced automation, this system ensures efficiency, accuracy, and safety for industries like chemicals, oils, food, pharmaceuticals, and more.
Key Features
Touchscreen HMI (Human-Machine Interface)
Intuitive Controls: Easy-to-use color touchscreen for setting recipes, batch sizes, and monitoring fill processes.
Recipe Management: Store multiple product profiles (e.g., flow rates, target weights) for quick selection.
Real-Time Data: Displays fill volume, weight, and error alerts during operation.
Full Automation
Automatic Conveyor: Roll-in/roll-out conveyor system for seamless drum loading/unloading.
Servo-Controlled Nozzle: High-precision filling with adjustable flow rates for thin or viscous liquids.
Automated Seal/Cap: Optional integrated lid sealer for tamper-evident closures.
High-Speed Precision Filling
Speed: Up to 60 drums per hour (dependent on product viscosity and container size).
Accuracy: ±0.1% filling accuracy via high-precision load cells and weight-based control.
Drift-Free Cutoff: Eliminates overfilling and dripping during nozzle retraction.
Safety & Compliance
ATEX/IECEx Certification: Safe for hazardous environments (Zone 1/21).
Static Grounding & Nitrogen Blanketing: Prevents sparks and oxidation in flammable products.
Interlocked Safety Doors: Ensures no access during operation.
Spill Tray & Containment: Catches leaks or drips for easy cleanup.
Customizable Options
Product-Specific Nozzles: For oils, chemicals, or high-viscosity fluids.
Integrated LN2 Cooling: Prevents vapor buildup in flammable liquids (optional).
Batch Tracking: Barcode/RFID scanners for traceability and inventory management.
Advanced Technology
Inline Filters: Removes contaminants from the product stream.
Vacuum Purging: Minimizes product waste during nozzle purging.
Ethernet Connectivity: Integrates with MES/ERP systems for data logging and analytics.
Durability & Materials
Stainless Steel Construction: 316L grade for corrosion resistance and compatibility with aggressive chemicals.
Chemical-Resistant Hoses & Seals: Long lifespan even with harsh products.
Technical Specifications
Filling Range: 2–200 liters per drum.
Speed: Up to 60 drums/hour (dependent on product viscosity).
Accuracy: ±0.1% of target weight.
Materials: 316L stainless steel (optional Hastelloy for extreme corrosion resistance).
Power: 220V/50Hz or 110V/60Hz (energy-efficient motors).
Certifications: ATEX/IECEx, CE, ISO, NSF (food/pharma models).
Applications
Chemicals: Solvents, acids, bases, and specialty chemicals.
Oils & Lubricants: Engine oil, gear oil, grease, and industrial lubricants.
Food & Pharma (Optional): Edible oils, pharmaceutical syrups, and APIs.
Industrial Fluids: Diesel, fuel additives, and water treatment chemicals.
Cleaning Products: Detergents, disinfectants, and surfactants.
Operation Steps
Load Drum: Roll the drum onto the conveyor and position it under the filling nozzle.
Select Recipe: Use the touchscreen to choose the product, fill volume, and flow rate.
Automated Filling: The system lowers the nozzle, purges air, and fills to the target weight.
Sealing & Verification: Nozzle retracts, and the system confirms weight/volume accuracy.
Unload & Repeat: Conveyor rolls the filled drum away for sealing or labeling.
Benefits
User-Friendly Operation: Touchscreen controls simplify setup and reduce training time.
Consistent Quality: High-precision filling ensures uniformity and reduces waste.
Safety: ATEX certification, static grounding, and interlocks minimize risk in hazardous environments.
Scalability: Customizable for small batches or high-throughput production lines.
Data Integration: Ethernet connectivity enables integration with MES/ERP systems for traceability.
Why Choose This System?
This Smart 200L Drum Filling System combines touchscreen convenience, fully automated operation, and precision filling for superior performance in industrial settings. Its robust design, compliance with international standards, and customizable features make it ideal for businesses seeking efficient, reliable, and safe filling solutions.
Contact us for a tailored quote or demo!
Immediate Order:
Website: http://www.otgqoql.cn/product/drumfillingmachines-en.html
China Manufacturing Co Ltd.: https://fillingmachinecn.en.made-in-china.com
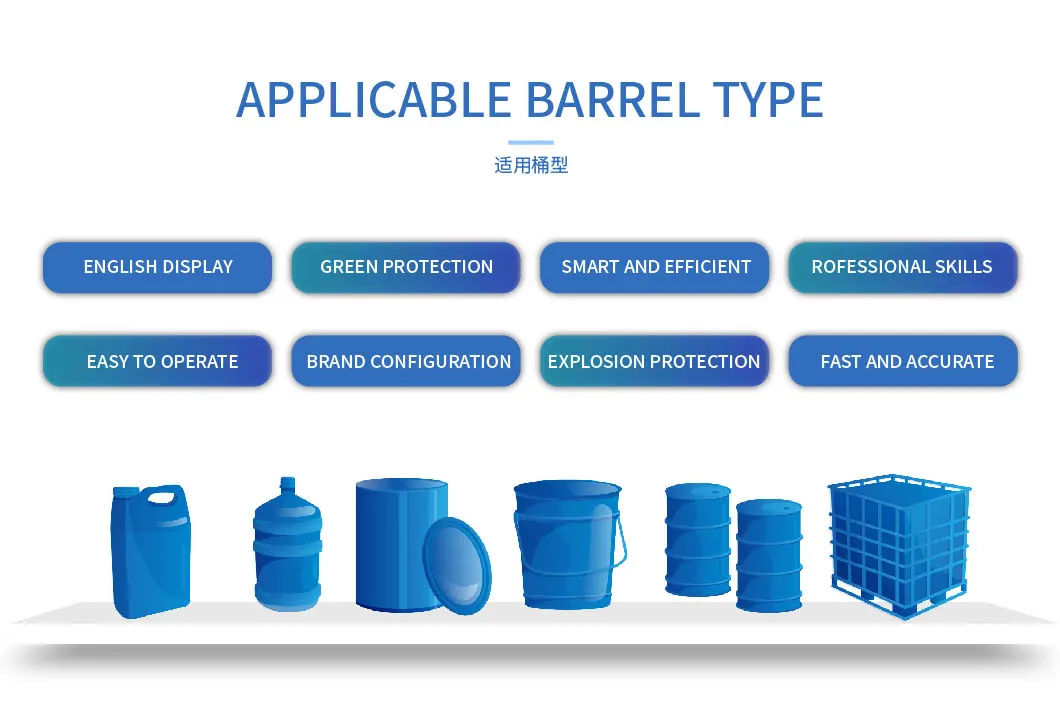
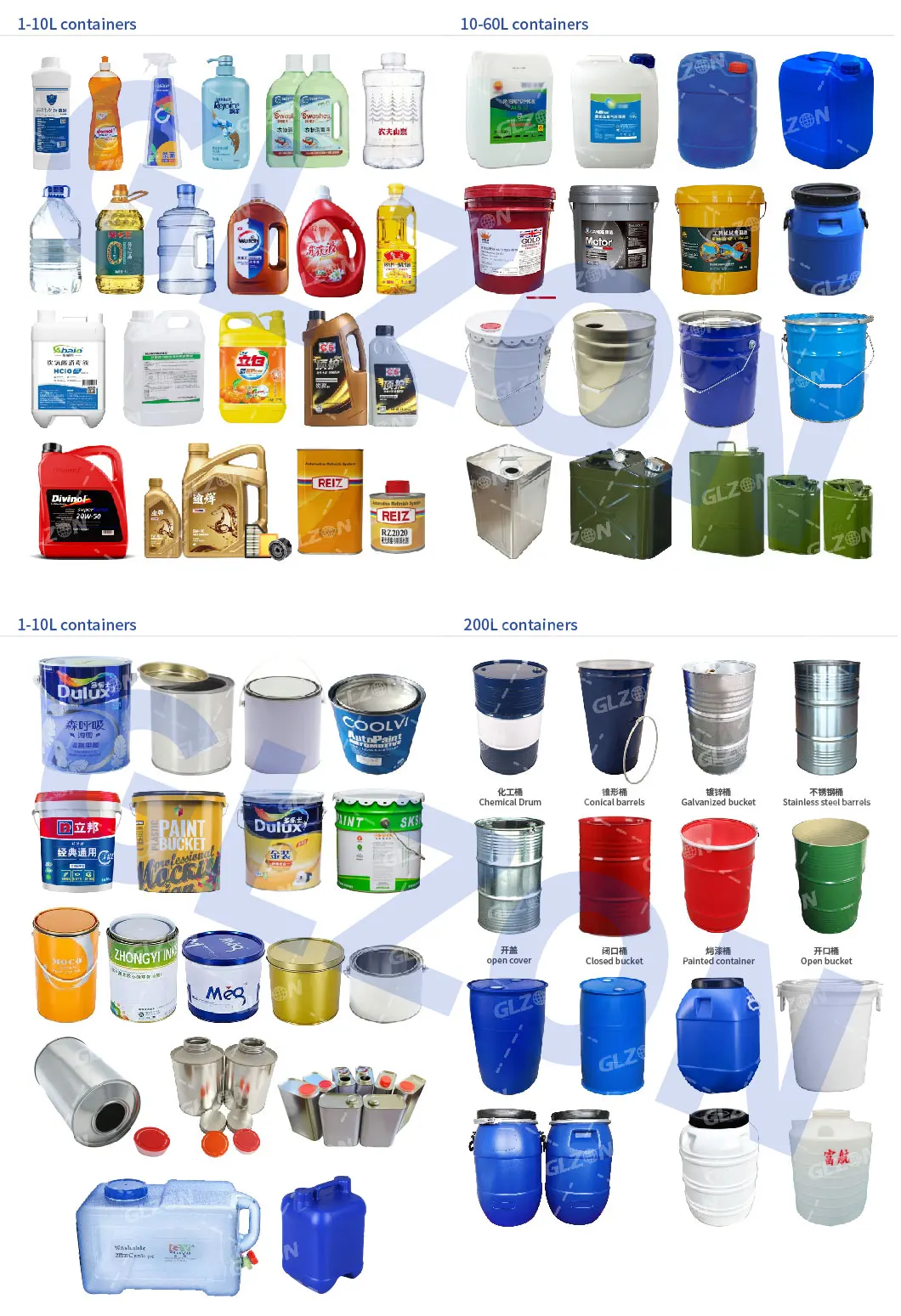
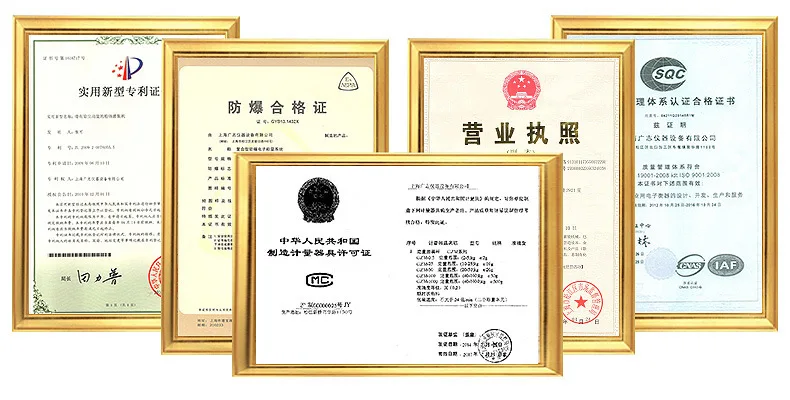
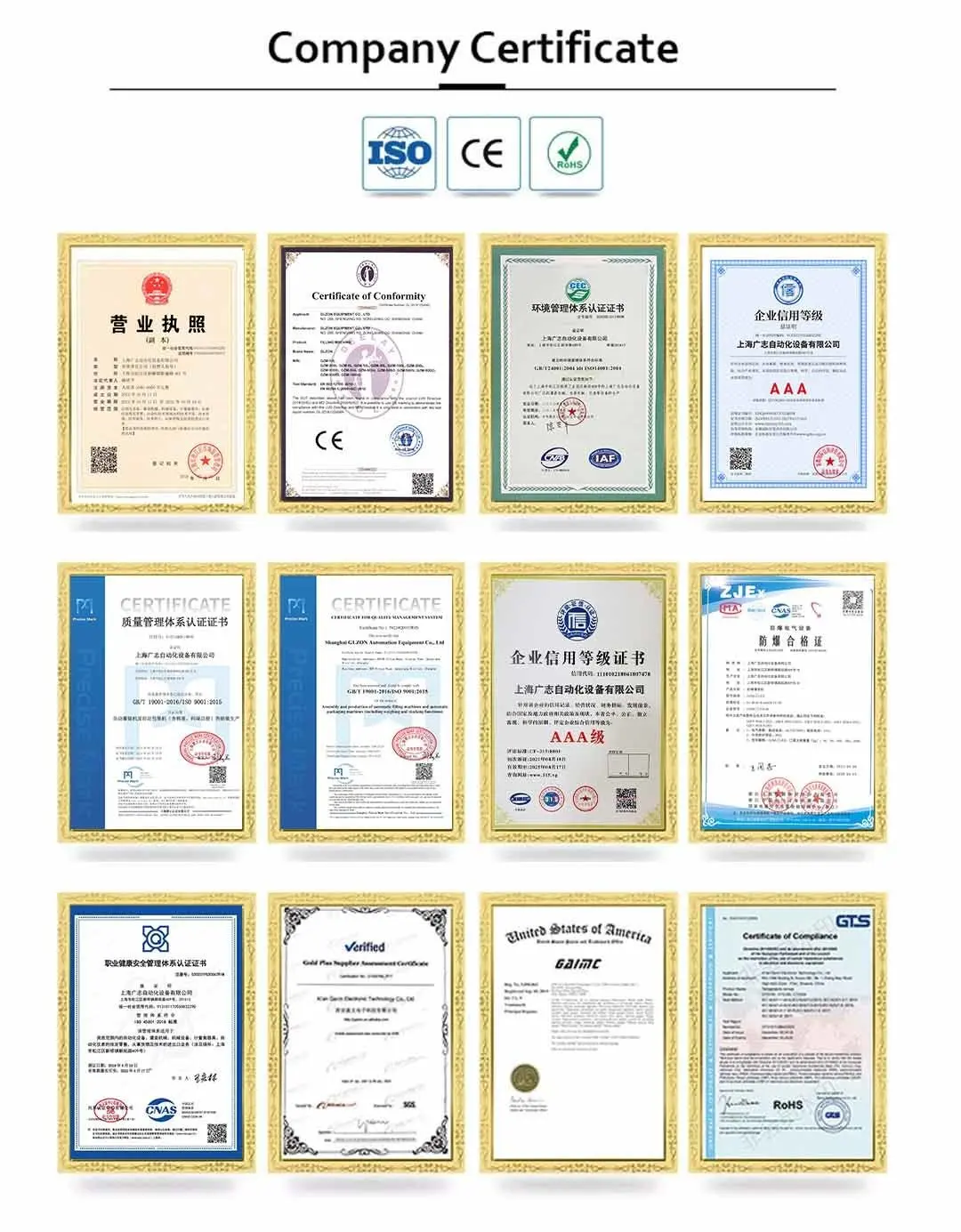
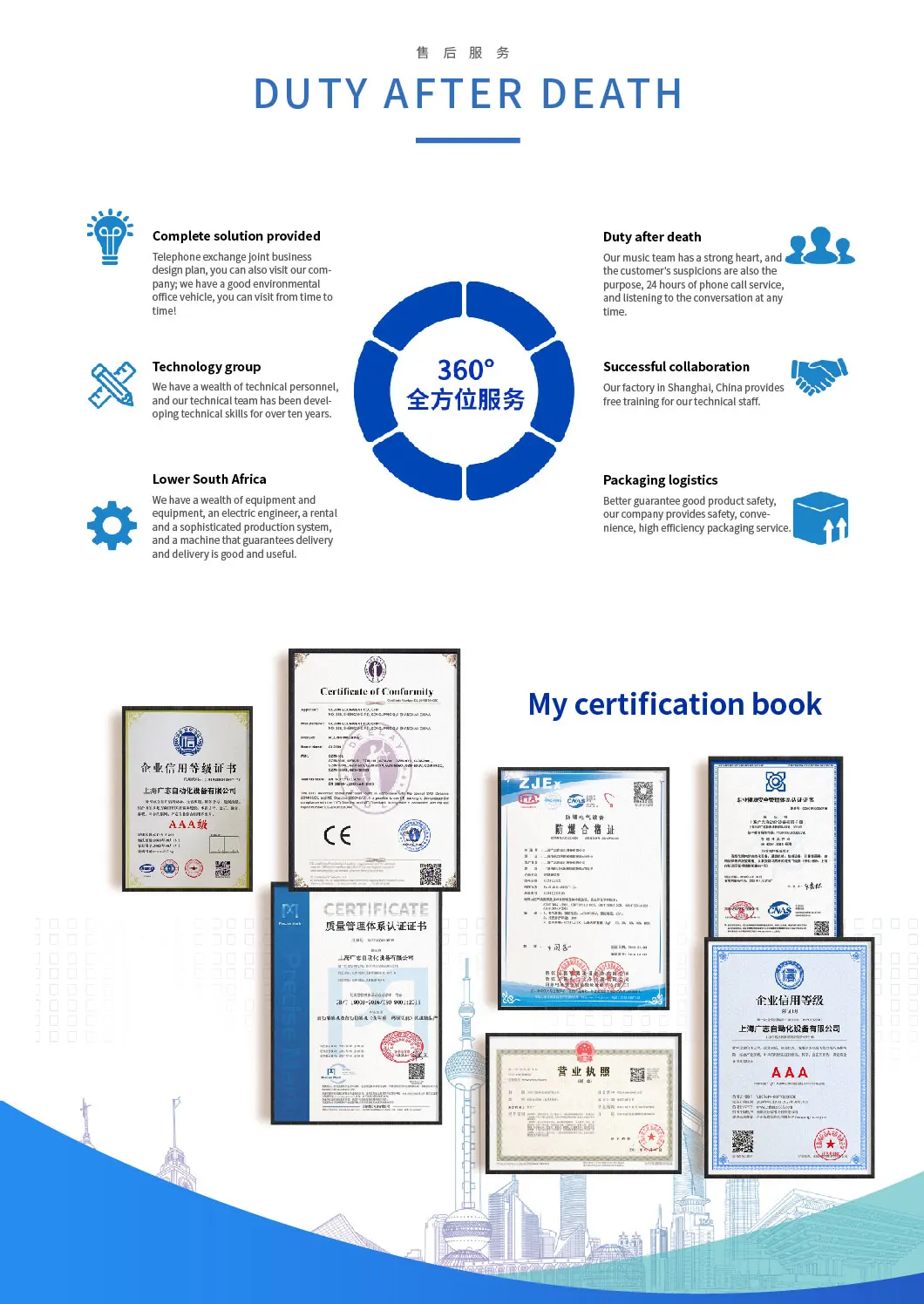
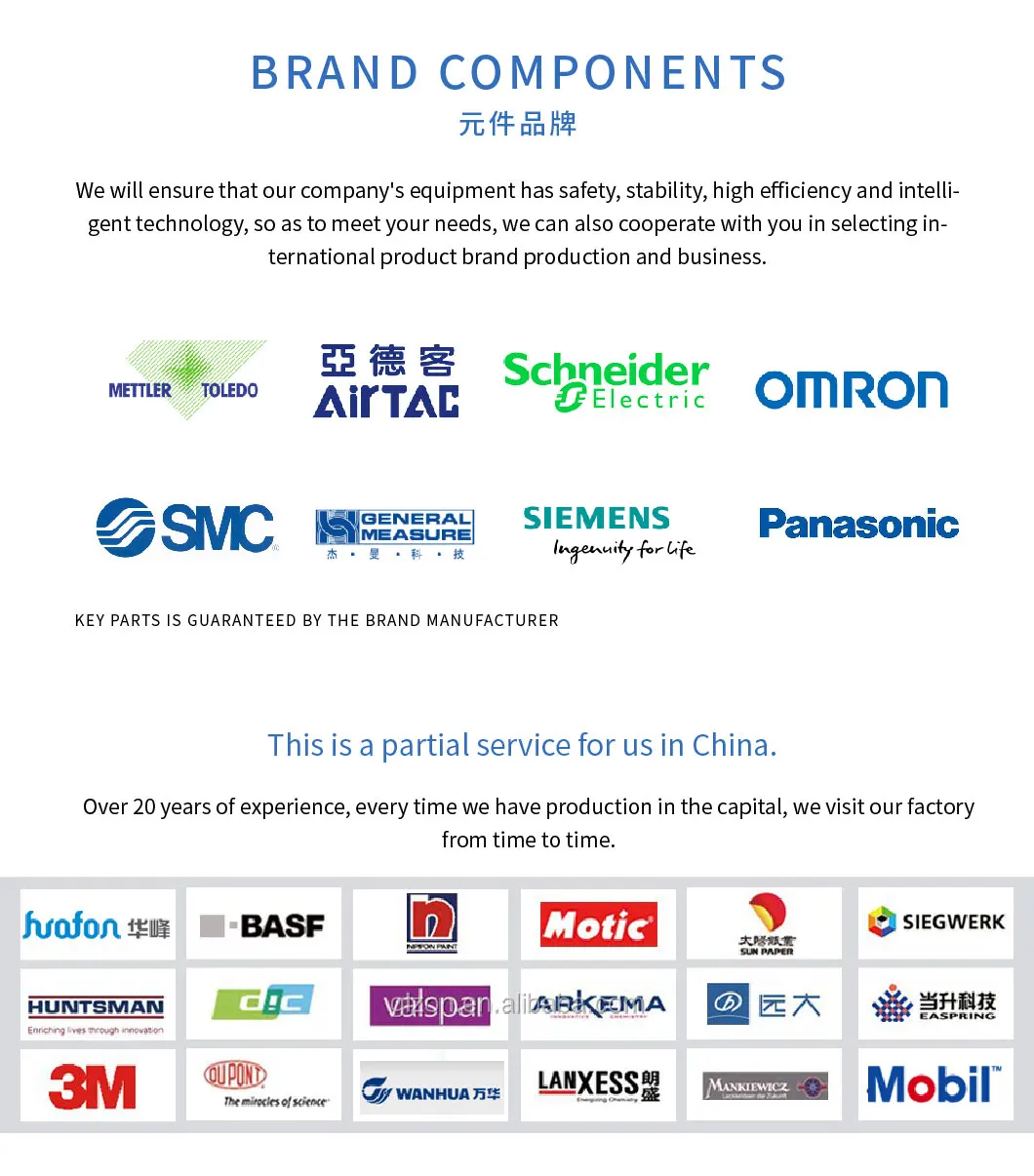
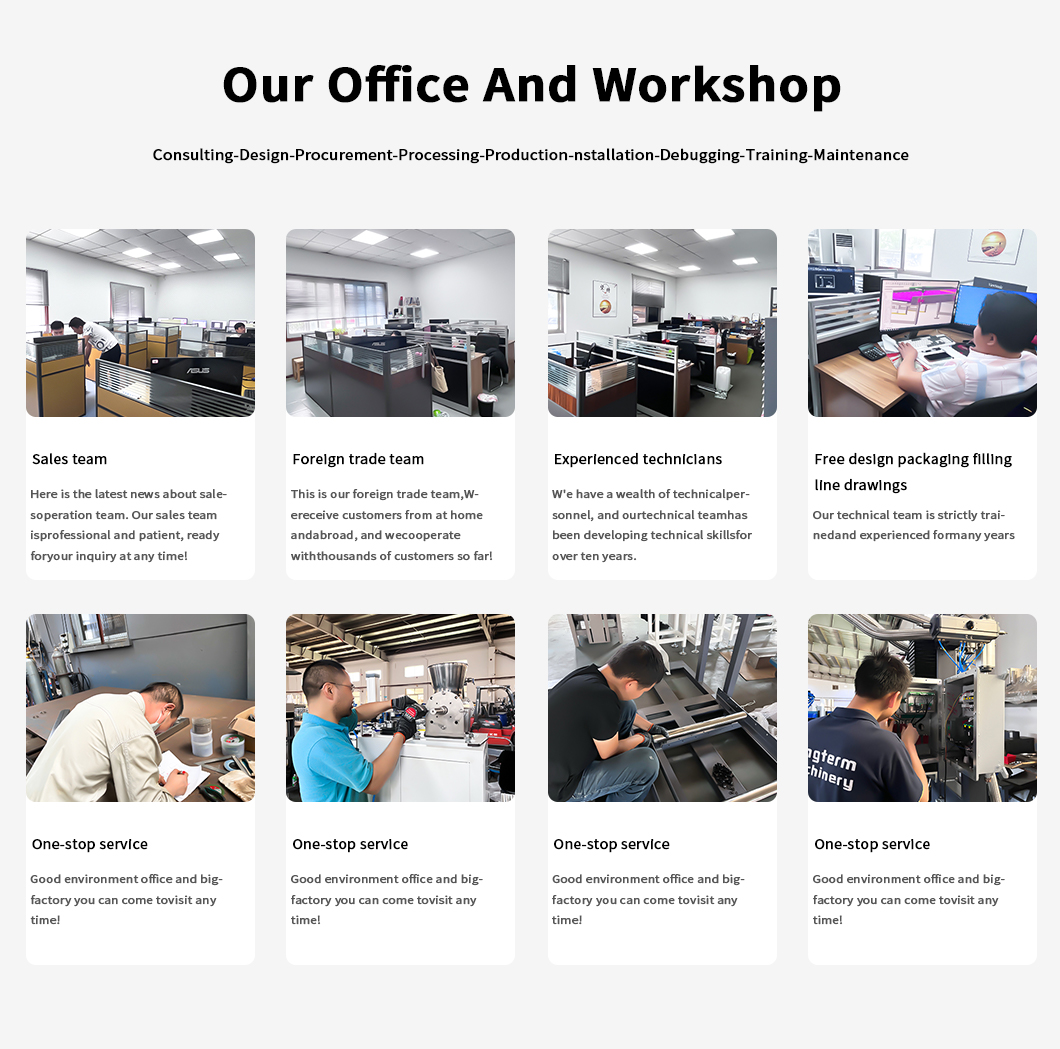
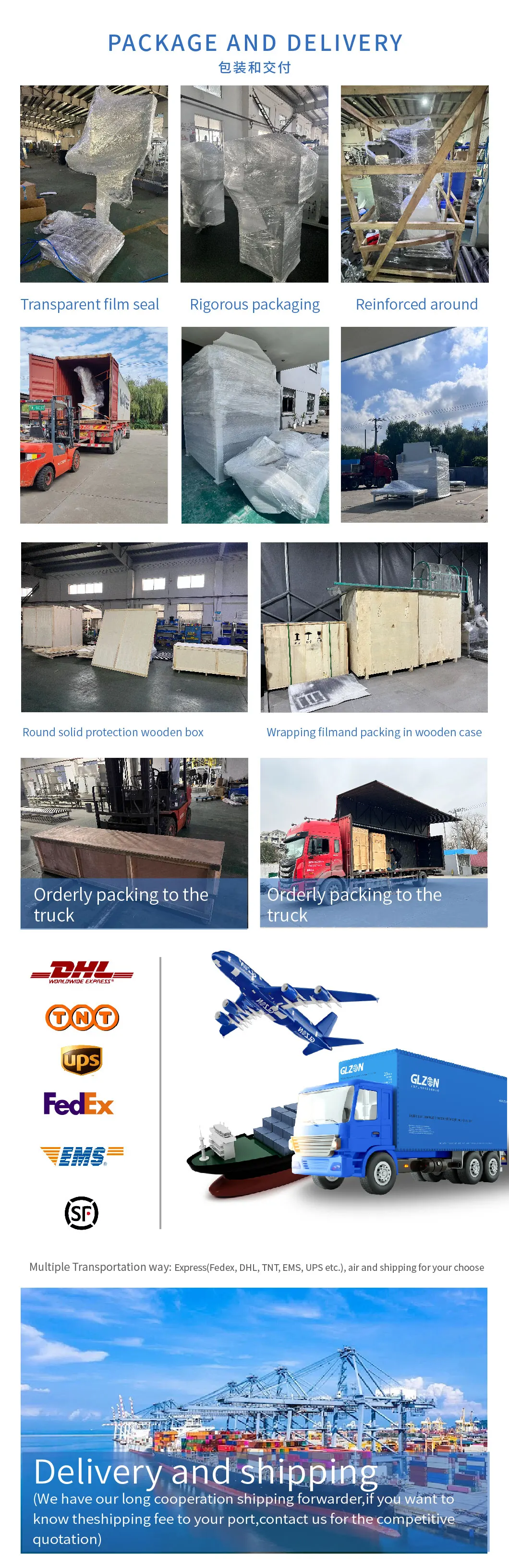
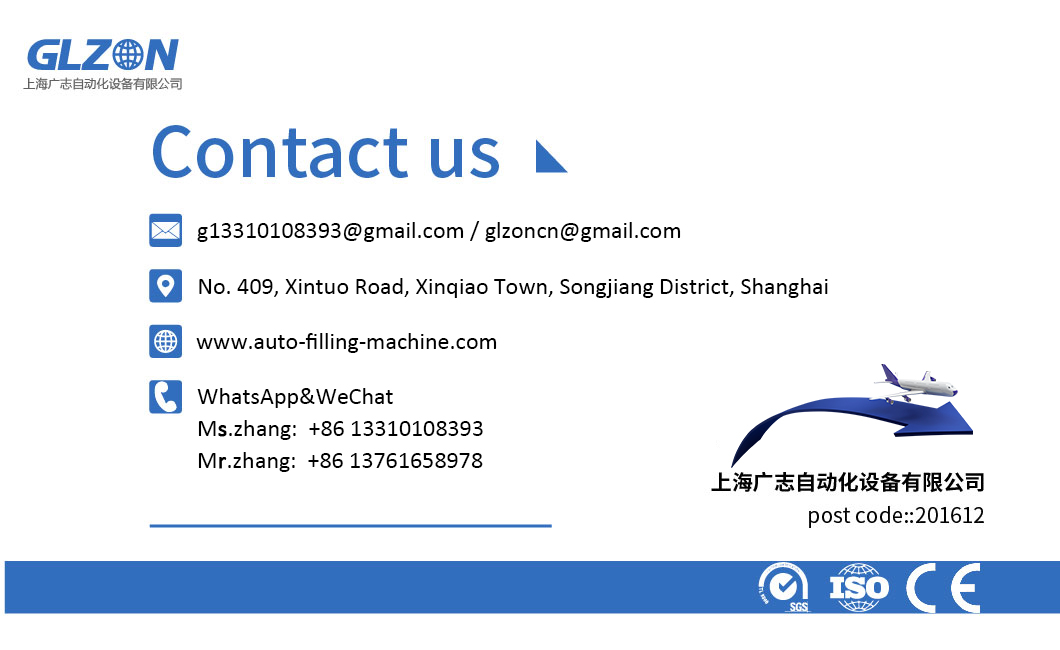